Preforms, Rings, LayerMet
Aufhauser Rings, Strips, Shims, Washers, Discs, Edgewounds, Cut-offs, and Custom Shapes are available for all of your specific applications.
With continuing trends toward mechanizing or automating the brazing process, brazing alloys made to various forms and sizes are your solution to pre-placement requirements.
When brazing filler material is to be preplaced it should be located at the part of the joint that is last to reach brazing temperature. This ensures that when the filler alloy melts the molten material will be drawn through the joint by the combined effects of capillary flow and temperature gradient.
Aufhauser manufactures and supplies brazing preforms with pre-determined, consistent and uniform shapes that melt at very low, tightly-controlled temperatures. These manufacturing qualities ensure smooth operations on automated brazing equipment. Aufhauser brazing preforms assure the operator of consistent brazing performance with every application, every batch. Operators no longer need to adjust heating practice from one batch of brazing rings to another to achieve uniform results. The advantage of this precise control is also readily apparent in automated brazing operations where tight control of flow temperatures can significantly reduce the incidence of rejects.
Rings
Advantages of using preform rings over hand-fed alloy:
- Improved process - alloy is applied to the joint prior to heating, simplifying the brazing process and reducing re-working or scrapping.
- Quality indication - joint is complete when the alloy is visible at the top of the joint/seam.
- Consistent alloy volume - preformed ring provides the joint with a known volume of alloy, eliminating excess waste and improving joint quality.
- Fewer joint voids - use of rings results in better quality, consistent circumferential joints with fewer potential field failures.
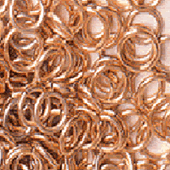
ID Rings - a complete turn of wire, butt-end and flat-plane.
Gap Rings - Also known as O.D. rings, gap rings are designed to be slightly oversized with a specified gap at the end of a full turn of wire. This gap provides some flexibility in compressing the ring to fit within a tube and to hold its position within the tube during brazing. (For example: placing the ring within the female tube end, and sliding it in with the male tube end.) Packaged on a tube to prevent tangling.
Segment Rings - Also known as arc rings. With less than a full turn form (210 - 250 degree arc), segment rings are ideal for applications where components are pre-assembled. The segment ring can be snapped into place, and ring wire diameter is specified to provide adequate volume for the entire braze joint.
Multi-turn Rings - From 1-1/16 to 3+ full turns. Use multi-turn rings when the joint requires a small-diameter wire ring for which additional volume is required, or when mechanical flexibility of an overlap ring is desired.
TABLE: QQ-B-654 Grade III 150-1500 PSI Silver Brazing Band Rings - BCup5
Nominal (In.) | Tolerance (In.) | Silver Factor (Toz/ kpc) |
Copper Factor (lb/ kpc) |
Total Weight (lb/ kpc) |
||||||
---|---|---|---|---|---|---|---|---|---|---|
IPS | OD | THK | WTH | OD | THK | WTH | Gap | |||
0.5 | 0.949 | 0.04 | 0.078 | 0.949/0.969 | 0.037/0.043 | 0.075/0.081 | 0.073/0.130 | 5.9069 | 2.15974253 | 2.699695 |
0.75 | 1.179 | 0.05 | 0.094 | 1.179/1.199 | 0.047/0.053 | 0.091/0.097 | 0.073/0.130 | 11.0518 | 4.04087395 | 5.051124 |
1 | 1.444 | 0.05 | 0.125 | 1.444/1.464 | 0.047/0.053 | 0.122/0.128 | 0.073/0.135 | 18.1461 | 6.63477646 | 8.29352 |
1.25 | 1.789 | 0.05 | 0.125 | 1.789/1.809 | 0.047/0.053 | 0.122/0.128 | 0.073/0.135 | 22.6371 | 8.27681224 | 10.346 |
1.5 | 2.031 | 0.05 | 0.188 | 2.031/2.051 | 0.047/0.053 | 0.185/0.191 | 0.073/0.135 | 38.7841 | 14.18064 | 17.726 |
2 | 2.506 | 0.05 | 0.188 | 2.506/2.526 | 0.047/0.053 | 0.185/0.191 | 0.073/0.135 | 48.0836 | 17.580844 | 21.976 |
A Method of Calculating Diameter of Wire of the Ring
The optimum volume of filler material needed to fill a sleeve joint may be determined as follows:
D = 1.27 × √ (L × G )
D = Wire diameter of the ring
L = Length of the joint
G = Radial joint gap (at brazing temperature)
This formula will result in the wire diameter that provides sufficient material in the ring to form a small fillet at either end of the joint during brazing. Use "worst-case" (maximum) tolerances for L and G.
TABLE: Sample Derived Values of Recommended Wire Diameter for Preformed Rings in Relation to Joint Length and Radial Joint Gap
Radial Joint Gap "G" (mm) | |||||||
---|---|---|---|---|---|---|---|
Joint Length "L" (mm) | 0.05 | 0.075 | 0.100 | 0.125 | 0.150 | 0.175 | 0.200 |
2.0 | 0.40 | 0.50 | 0.60 | 0.65 | 0.70 | 0.75 | 0.80 |
4.0 | 0.60 | 0.70 | 0.80 | 0.90 | 1.00 | 1.05 | 1.15 |
6.0 | 0.70 | 0.85 | 1.00 | 1.10 | 1.20 | 1.30 | 1.40 |
8.0 | 0.80 | 1.00 | 1.15 | 1.25 | 1.40 | 1.50 | 1.60 |
10.0 | 0.90 | 1.10 | 1.25 | 1.40 | 1.55 | 1.70 | 1.80 |
12.0 | 1.00 | 1.20 | 1.40 | 1.55 | 1.70 | 1.85 | 1.95 |
14.0 | 1.10 | 1.30 | 1.50 | 1.70 | 1.85 | 2.00 | 2.10 |
See Standard Pipe Size reference tables
Washers
Stamped - Stamped brazing washers are specified with O.D. and I.D. dimensions and are made from strip with a typical thickness range of 0.0015 to 0.010". Square or rectangular washers may be substituted when O.D. is not specified. Commonly used in the electronics industry where most brazing is done in furnaces without flux, and where components are light weight resulting in minimal displacement.
Edgewound - Edgewound washers are made by winding flat wire on edge, resulting in no scrap waste. In the winding process, the O.D. is stretched while the I.D. is compressed, so certain physical limitations may apply.
Coined - When edgewound washers are not achievable, coined washers can be an option. These are formed by flattening a ring and result in no scrap waste.
Slugs
Where space and assembly configuration allow, brazing slug made of cropped pieces of rod or strip is an economical form of brazing alloy preplacement. Wire can be flattened slightly prior to cutting to temper roll tendency.
Other Forms
Wire forms - a variety of shapes such as rectangles, "u" clips, hairpins, oblong rings, etc.
Stamped forms - flat or curved, irregular shapes such as ovals, rectangles, shims, plain or perforated strip.
For custom preforms, contact us with your specifications:
Configuration | Required Dimensions |
---|---|
Disc | OD, Thickness |
Rings | OD, Wire diameter, Gap |
Shims | Length, Width, Thickness |
Washers | OD, ID, Thickness |
Wire Segments | Length, Diameter |
Layered Alloys
For applications where carbide is brazed to steel, it is often desirable to use a multi-layer brazing alloy with a copper center, Aufhauser LayerMet. The copper serves as an absorber of thermal expansion as well as shock. Some of Aufhauser SilverAlloys are available as strip and stamped preforms.
Aufhauser LayerMet (a silver-copper-silver "sandwich") should be used to braze large carbides to steels or stainless steels. By "large" we mean greater than 0.5 sq. inch (12.7 mm²). When brazing with LayerMet, the silver on each side of the sandwich bonds with the carbide and the steel. The copper in the middle (which melts at a higher temperature) acts to relieve the stresses caused by unequal rates of thermal expansion of the joined metals.
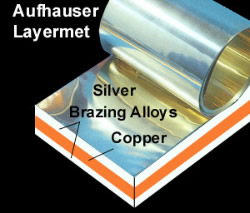
View Aufhauser LayerMet products